Pump Chemicals Safely With an AODP
UK based manufacturer of speciality chemicals has reduced its pump maintenance time from half a day to less than half an hour, using a 'one nut', polypropylene Air-Operated Double-Diaphragm Pump from Flotronic.
The 500 series Polypropylene pump was chosen to replace an existing diaphragm pump, from another supplier, which proved cumbersome to maintain in the event of a breakdown. They are now able to change a failed diaphragm in less than twenty minutes, simply by removing a single nut - therefore achieving major savings through reduced downtime.
To manufacture its range of speciality proteins, the company needed a 1.5 inch pump that could handle aggressive chemicals. As the company's processes typically involve the pumping of hydrochloric acid, caustic soda in tandem with liquid flavourings - safety was a major consideration.
"The safe, Air-Operated Double-Diaphragm design was a major attraction of the one-nut pump,"
"In the event of a diaphragm rupture, a single diaphragm design can pump out aggressive liquids, via the exhaust system. The design of the 500 series prevents this risk of contamination, by containing the liquid inside the pump."
This is due to the Flotronic Guardian diaphragm rupture protection barrier – which, in the event of a diaphragm rupture, contains the media within an intermediate chamber. For added safety, a Sentinel alarm system has been specified to quickly alert operators in the event of diaphragm failure.
PROCESS DETAILS
- Aggressive chemicals such as hydrochloric acid (36%) & caustic soda (32%)
- Flowrate up to 60 gpm
- Temperature up to 80C
- Pressures up to 7 bar
PUMP DETAILS
- 500 Series Polypropylene
- Model F33PPTTPEBSP
- PTFE elastomers
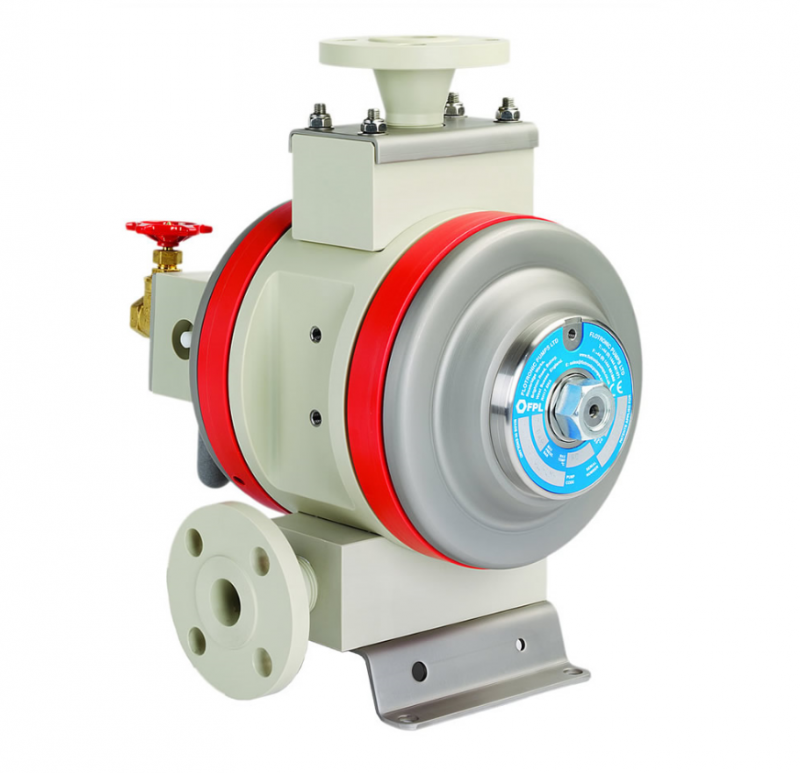